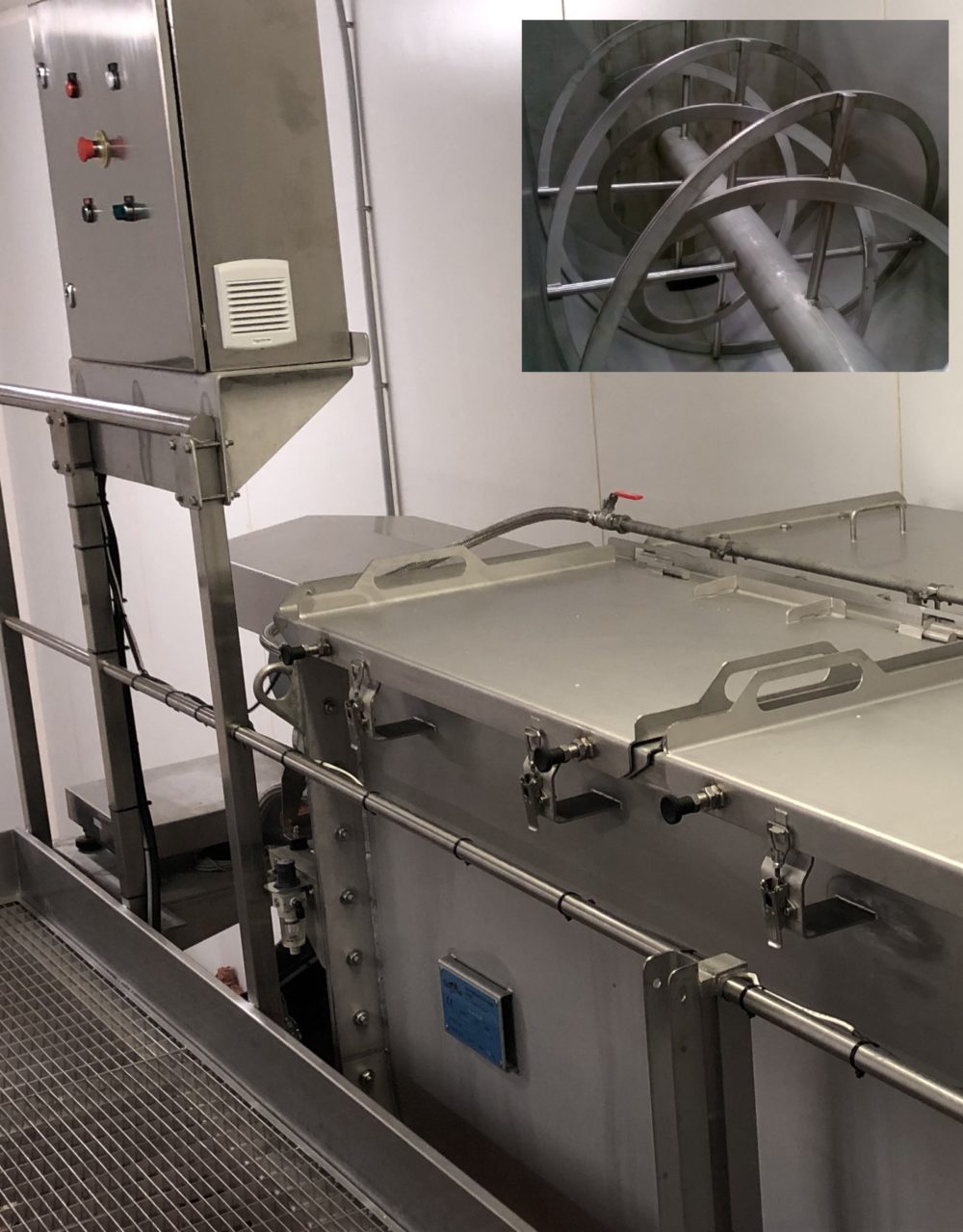
Horizontal mixers
Horizontal batch mixers come in different types (double ribbon, ploughshare, paddle, etc.) are recommended for accurate and fast mixing of dry and wet materials. Based on a back and forth movement of the materials within the tank, their rotors are designed on a case-by-case basis to guarantee a homogeneous and high quality mixture. Intended for successive batch production, this type of mixer can be equipped with one or more manually or automatically operated drain valves, which can be positioned on demand;
With a capacity of up to 6,000 litres, these mixers can be equipped with a multitude of options: sprayer and/or washer booms, weighing, access hatches, level detector, etc. Based on a bottom-up movement, these mixers are used to deagglomerate and stir products most often coming from superimposed layers.
With a capacity of up to 50m3, these mixers can be equipped with a multitude of options: sprayer and/or washer booms, weighing, access hatches, level detector, etc.
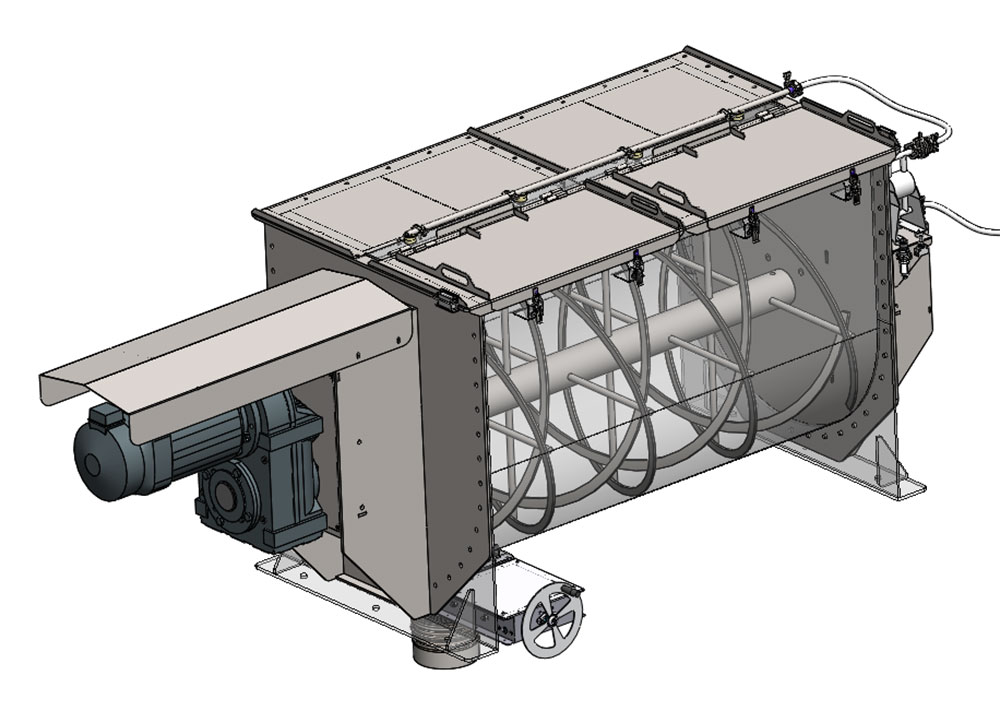
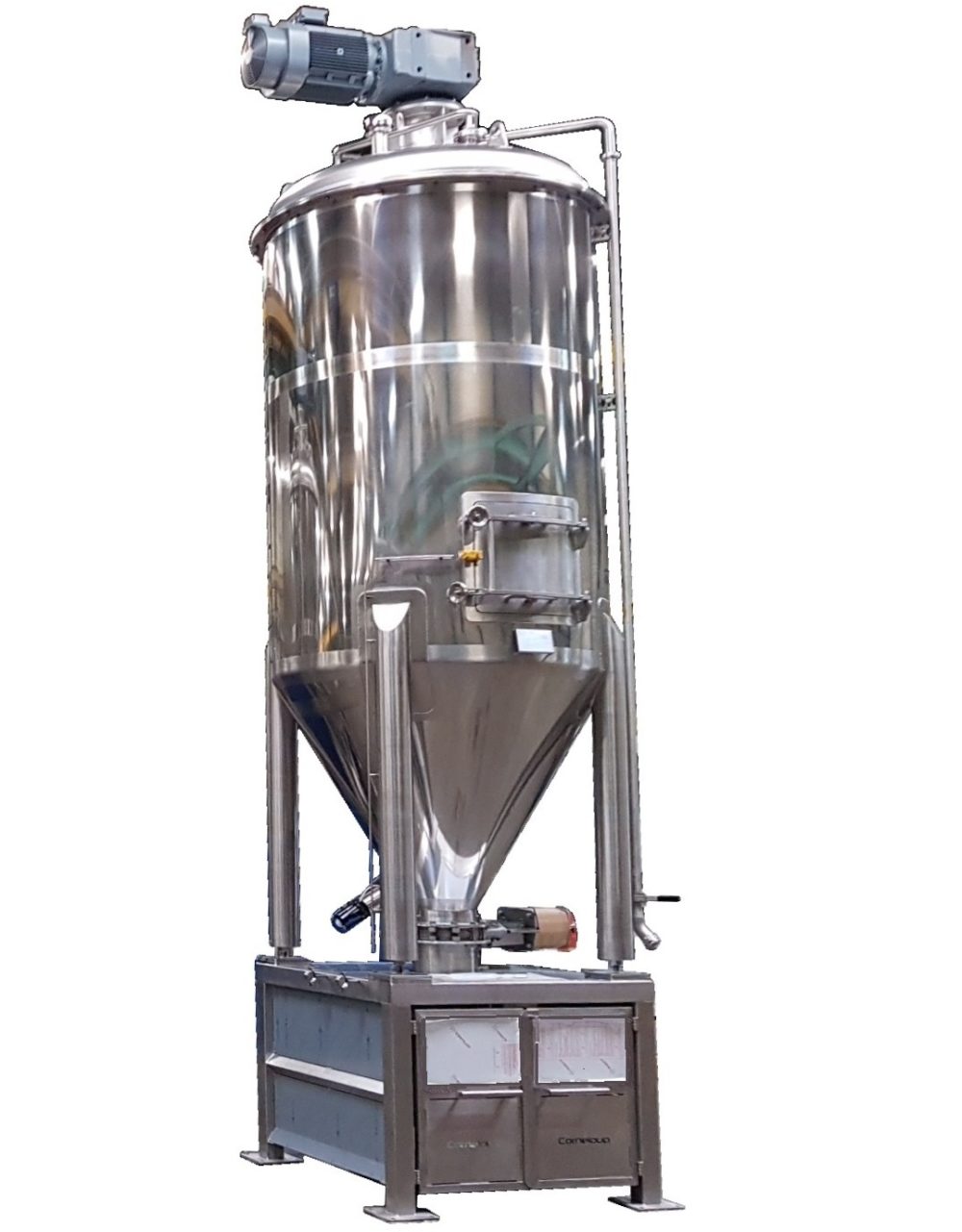
Vertical mixers
Used to homogenise powders and granules in large capacities, this cylindro-conical mixer, equipped with a vertical conical screw progressive-pitch rotor, sheathed or not, allows the materials to be gently mixed to preserve their integrity.
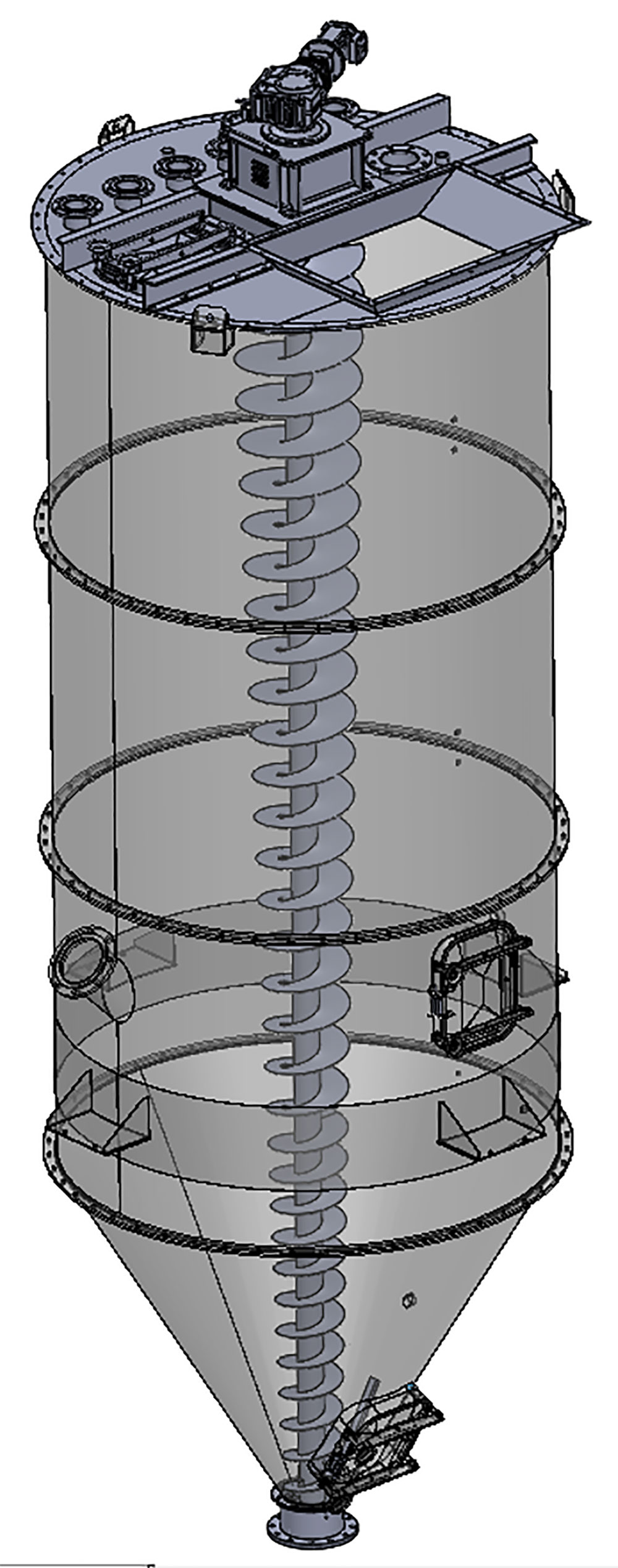
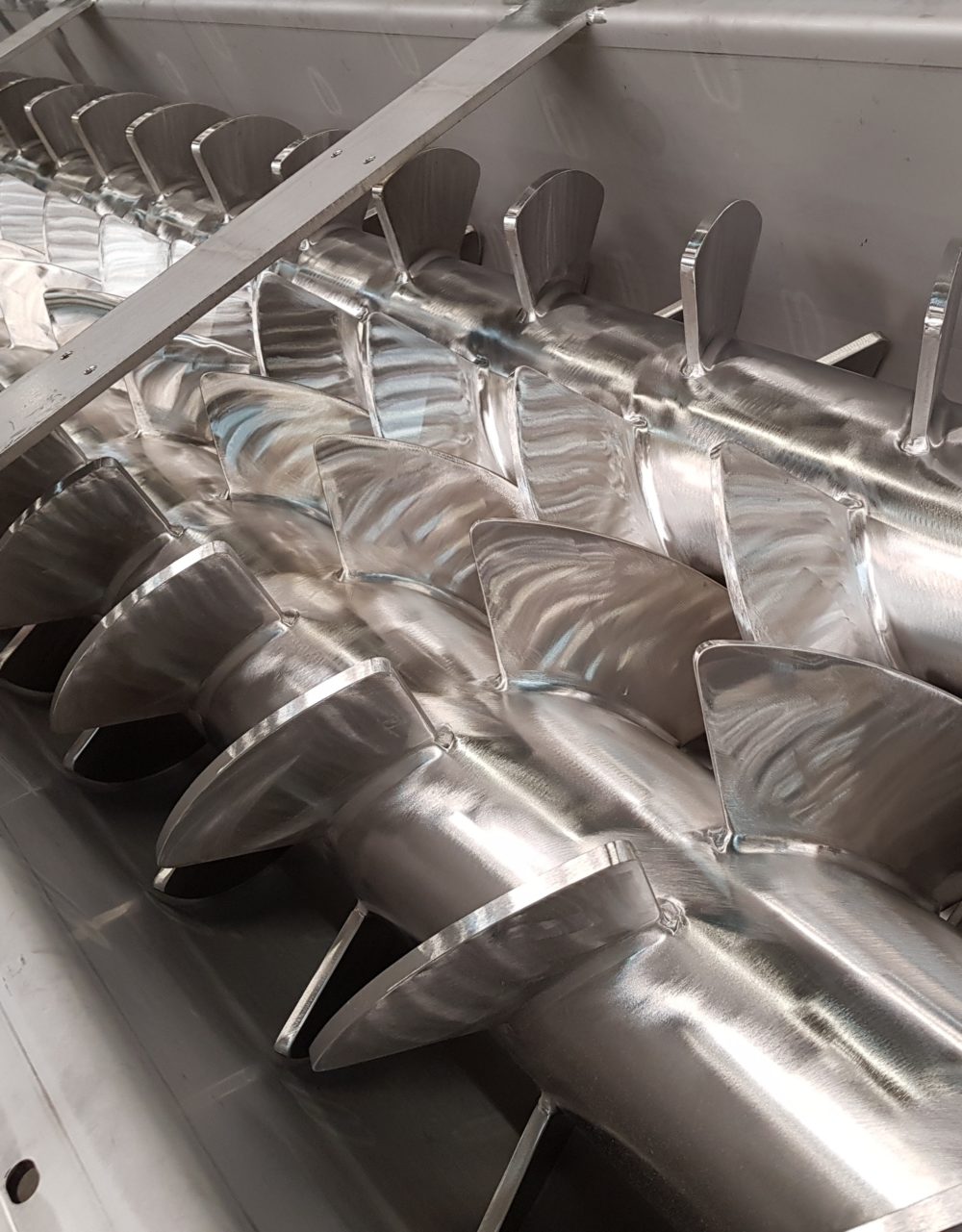
Continuous mixers
Unlike batch mixers, these mixers, based on the principle of screw conveyance, allow, in a single piece of equipment, several products to be mixed and this mixture to be continuously transferred to the equipment’s outlet.
To do this, the ergonomics and the dimensioning of the rotor(s) are studied on a case-by-case basis, according to 3 main
inseparable criteria:
- Meeting the constraints linked to the very nature of the components to be mixed (dry, powdery, wet, abrasive, etc.)
- Optimising the residence
time required for homogenisation of the mixture (longer or shorter mixing chamber, use of several rotors, secant or non-secant...) - Ensuring the required flow rate (mixing chamber volume)
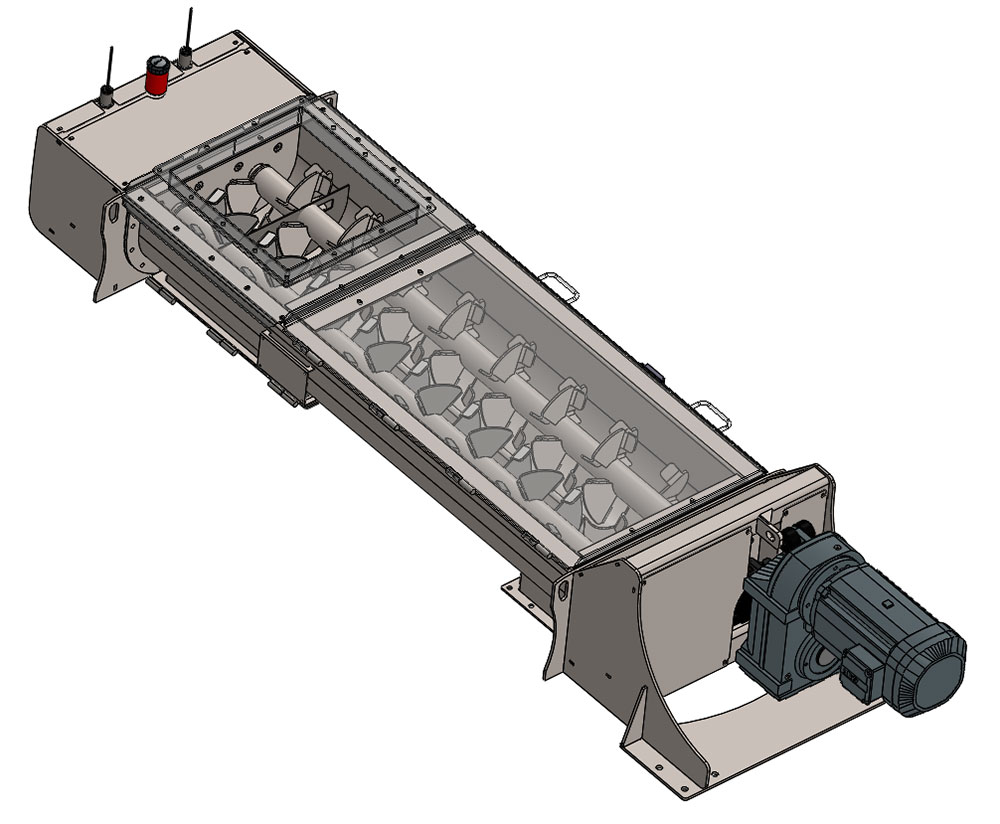